What control towers can do for your supply chain
More than an ‘old-fashioned’ freight management desk, a control tower offers functionalities which, if used well in appropriate situations, can certainly add value to logistics and supply chain operations.
Control towers are springing up across global supply chains, to go by trade media articles and news from third-party logistics providers (3PLs). Anyone who is in the supply chain arena has at least one, if not several.
The control tower concept is easy to visualise: a hive of activity staffed by multilingual traffic controllers, with its central point as a vast screen showing an integral overview of all freight flows, clearly pinpointing any problem areas.
But is that really what a control tower is about? More than an ‘old-fashioned’ freight management desk, a control tower offers functionalities which, if used well in appropriate situations, can certainly add value to logistics and supply chain operations.
What are control towers?
To understand what a control tower is, here is a summary of what it is not:
- It is not actually a tower.
- It is not in direct communication with truck drivers, sea captains or air pilots.
- It does not control the production, storage, replenishment and order process.
- It is not a synonym for a 4PL.
Control towers essentially provide supply chain visibility across divisions, countries and modalities.
The heart of a control tower is an information hub supported by a set of detailed decision-making rules and a trained team of operators. The big advantage of this central information hub is that it gathers and integrates data from various sources and then distributes it in a consistent, standardised format. This integrated overview allows the control tower operator to detect risks or opportunities at an early stage.
The actual scope of a control tower differs from one company to another, ranging from the orchestration of raw material supplies to a factory, to an end-to-end control centre. Management of spare parts and returns is always done separately.
What is the difference between control towers and traditional freight or distribution management?
Control towers are not physically or hierarchically linked to one specific location, whereas traditional freight and distribution flows are managed from either origin or destination.
Furthermore, control towers are usually focused on ‘event management’: they collect and store status information from suppliers and logistics service providers in a structured way. This information is then used to provide control tower teams with insights into the actual status of orders, products in stock and shipments. This allows teams to make informed decisions when planning, monitoring and analysing supply chains.
In contrast, freight management only focuses on transport or distribution. Freight management activities typically including freight forwarding, tracking and tracing, as well as pickup and delivery scheduling.
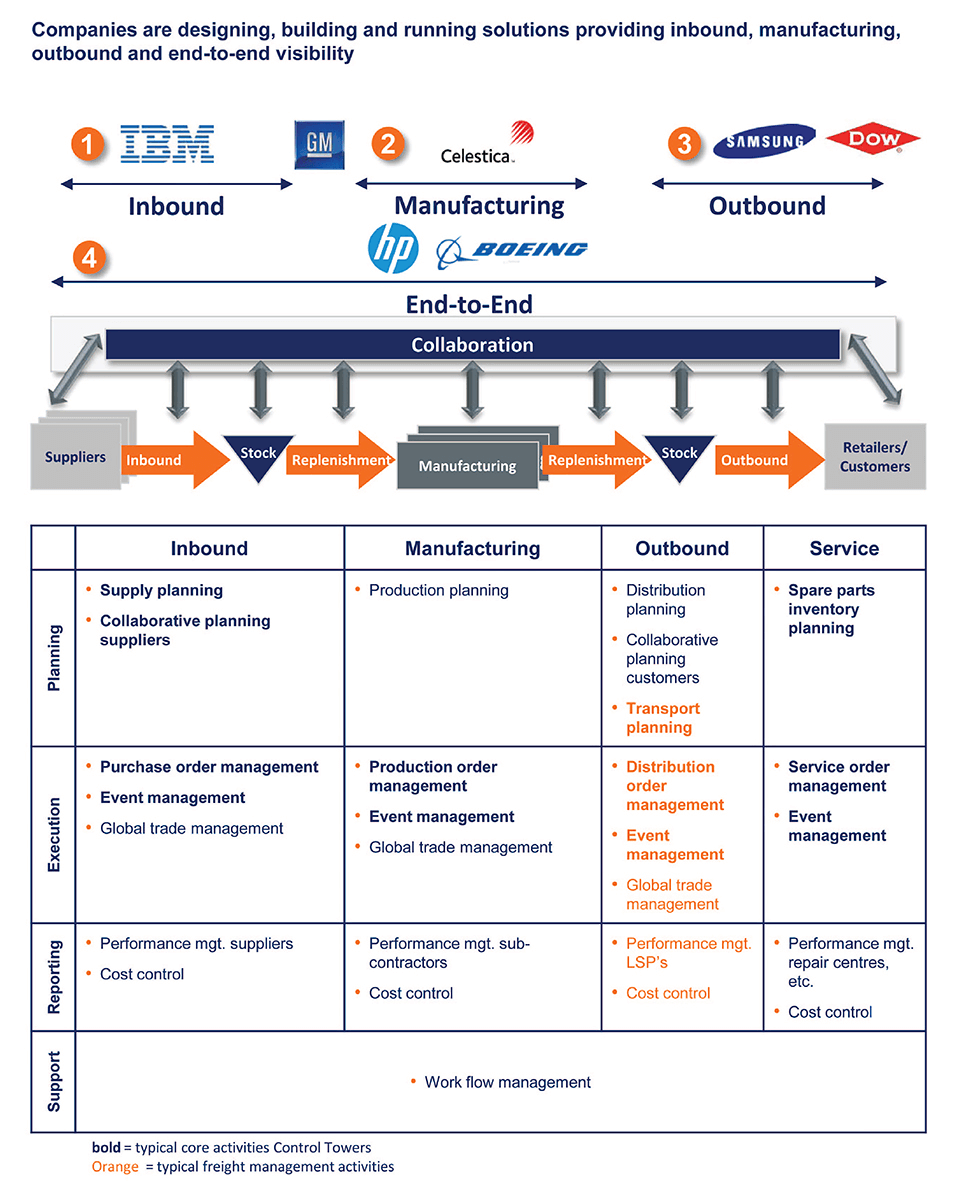
Who needs control towers?
Control towers are used to improve visibility in ‘complex’ supply chains. Your supply chain qualifies as complex when:
- The scope is global or inter/intra-continental
- The dependency is high
- Many supply chain activities are outsourced
- Your customers’ service requirements are increasingly challenging
Complex supply chains demand fast and fact-based information: the status of an order, the logistical costs of a product, the performance of a supply chain partner or a root cause analysis. Such information is needed to provide quick, integral responses to questions, and control towers with centralised data solutions are designed to do that.
Even highly fragmented supply chains can also gain significant benefits from control towers, as some DSV case studies show. Nevertheless, companies that are heavily structured around local organisations can expect some resistance when establishing a control tower. As with most centralisation efforts, local organisations will object to losing direct contact in their local language and to having reduced influence in ad-hoc problem-solving. If your local organisations currently have a large degree of independence, introduce a balanced scope and phased implementation to ensure sufficient local control combined with the benefits of a centralised approach.
Control towers can improve visibility in complex and highly fragmented supply chains by providing centralised data solutions and fast, fact-based information.
Can I set up a control tower internally or should I outsource it?
To set up and run a control tower, you need specific capabilities in:
- Planning: staff with a background in supply chains
- Event management: staff with a background in transport operations
- Business intelligence: staff with a background in operational improvement
- Management of supply chain partners: staff with a background in 3PLs
- IT management: handling IT tools to exchange data with supply chain partners (suppliers, manufacturers, 3PLs and carriers) as well as internal system management to store the data in a structured way and provide information to support the control tower functions
Your decision on whether or not to outsource a control tower depends on these factors:
- If it is feasible to develop the above-mentioned operational and IT capabilities in-house
- The business case behind the investment required for an in-house solution vs. the indirect costs associated with outsourcing
- The volatility of the workload and the reaching of a certain critical mass
The tradeoff between the increased control and in-house expertise when insourcing a control tower needs to be precisely balanced with the increased flexibility that outsourcing offers. Depending on the scope and volume of typical control towers, you would require a small to medium-sized team of full-time staff to cover the skills listed above. You would need to ensure business continuity during holiday seasons, peak seasons or staff illness.
Insourcing, at least in the early stages, tends to favour process quality, whereas outsourcing provides a solution with greater long-term flexibility in relation to resources and systems.
Typical benefits of control towers
Control towers help keep situations under control and they enable action to be taken to prevent potential problems. Without central teams and integral overviews, a lot of time is spent on local fire fighting. Control towers can identify patterns in local issues and develop structural counter-measures based on processes that fit the big picture.
This would please supply chain managers, but be sure to assess the expected benefits carefully:
- Align expectations and take a reality check, not only internally but also externally towards providers.
- The benefits should form the basis of the setup in terms of processes, systems and resources.
Most of the benefits of control towers come from increased supply chain visibility. They enable better planning, decision-making, proactive event management, improvement of the performance of supply chain partners and more sophisticated supply chain analytics. You will be able to:
- Save on logistics costs
- Reduce inventory
- Improve service levels such as total cycle time and on-time delivery
Speak to our experts to find out more about how control towers can help improve and optimise your supply chain visibility.
Would you like to learn more?
Our experts are ready to help. Get in touch and we'll find the solution you need.
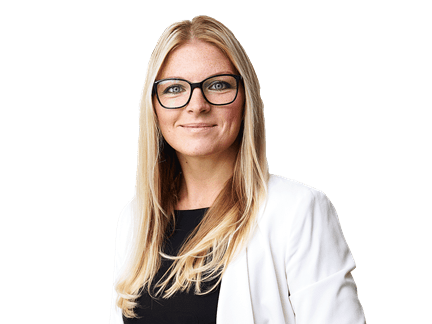